Manufacturing at WASSERMANN TECHNOLOGIE GmbH
– where quality is made
We think that in-house manufacturing leads to a different approach to design engineering and a different take on the optimization potentials of parts.
In-house manufacturing can also significantly reduce development times – and development is another key factor at WASSERMANN.
That is why we are quite proud of our manufacturing department, where, on over 3000 square meters, highly trained teams use modern machining centers, precision grinding machines, and precision measuring and test equipment to produce outstanding quality. And, by the way, we are also prepared for heavy jobs: We can safely handle parts and systems weighing up to 10 tons.
In-house manufacturing has always been the foundation of WASSERMANN.
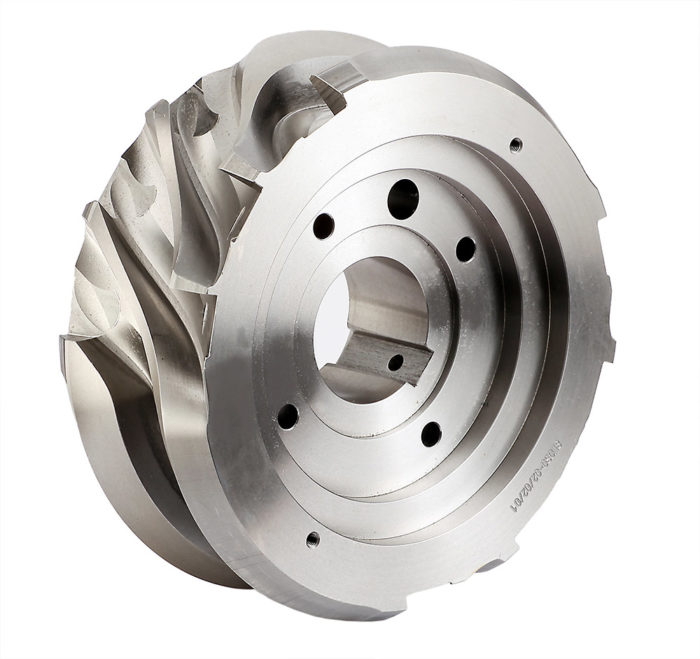
Manufacturing technologies at WASSERMANN TECHNOLOGIE GmbH
Automation
in our production- Hedelius BC 100/50 – existing system retrofitted with a TOOL-S tool terminal
- DMG Mori DMU 125P – fully equipped with a TOOL-D tool terminal from WASSERMANN
- Grob G350 and Grob G150 – complete automation with TOOL-D tool terminal and WORK-S pallet storage system
- Hyundai WIA LM 1800 – automation with robot cell WORK-R

Turning and mill-turning
Turning and milling machines
Ø
L
X
Y
Z
Automation
Index R 300
400
600
780
140
610
bar loader Ø 100
DMG CTX Gamma 2000 TC
630
2.050
630
200
2.050
DMG CLX 450
300
800
276
60
755
Index G420
400
2.300
800
340
2.300
Turning and milling machines
Ø
L
Automation
Gildemeister CTX 620
800
2000
Gildemeister CTX 510 eco V3
680
1050
bar loader Ø 76
SAEILO CONTUR H-66 P-3000
660
3000
Hyundai WIA LM 1800 TTSY
210
673
bar loader Ø 76, Terminal WORK-R
Facts & figures
- Diameter – 10 to 800 mm
- Length – length ratio < 5 x d
- Tolerances – 0.01 to 0.03 mm
Our turning shop
On our eight centers for turning and mill-turning, we machine any workpiece from very tine to pretty big. With modern automation and precise robot handling, we can produce parts quickly with high reproducible quality.

Milling and hard milling
Milling
5 sides
X
Y
Z
Automation
UNISIGN Uniport 600
✓
5.000
3.000
1.000
DECKEL MAHO DMF 360-II
3.600
1.100
900
DECKEL MAHO DMU 200 P
✓
1.800
2.000
1.100
DECKEL MAHO DMC 160 U
✓
1.600
1.250
1.000
DECKEL MAHO DMU 125 P -1
✓
1.250
800
800
DECKEL MAHO DMU 125 P -2
✓
1.250
800
800
Terminal TOOL-D
DECKEL MAHO DMC 100U
✓
1.000
1.250
1.000
HEDELIUS BC 100/50
3.500
1.000
770
Terminal TOOL-S
EMCOMAT FB-600
600
400
400
GROB G350
✓
600
855
755
Terminal WORK-S & TOOL-D
GROB G150
✓
450
670
665
Terminal WORK-S & TOOL-D
DECKEL MAHO DMC 160 U (2024)
✓
1.600
1.250
1.000
Terminal WORK-L & TOOL-D
Facts & figures
- Max. dimensions – 5000 x 3000 x 1000 mm
- Min. dimensions – 20 x 20 x 20 mm
- Tolerances – 0.02 to 0.08 mm
Our milling shop
Our manufacturing department runs up to 12 milling centers, some with 5-axis machining and with fully automated tool and pallet handling from WASSERMANN.
You can also trust us with large parts: The maximum workpiece dimensions are 5000 x 3000 mm. The tolerances are in the range from 0.04 to 0.08 mm.
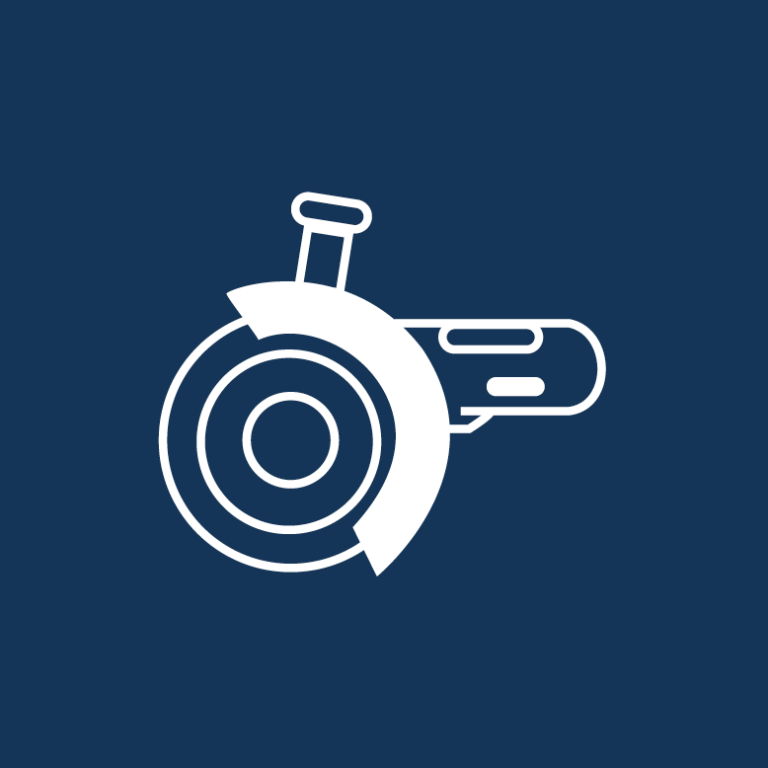
Grinding
Facts & figures
- Surfaces – up to Rz 0.8
- Tolerances – 0.01 to 0.02 mm
- Non-round grinding
Our grinding shop
WASSERMANN has seven units for flat, cylindrical, and non-round grinding.
We use these to machine surfaces with tolerances between 0.02 and 0.03 mm, achieving average roughness values (Rz) of up to 0.8.
Especially when producing non-round contours, the grinding process is what tips the scales. Where hard milling reaches its limits, grinding can achieve the required quality aspects for the performance and service life of a non-round profile.
We have decades of experience and the required grinding equipment to achieve the best possible non-round profiles.
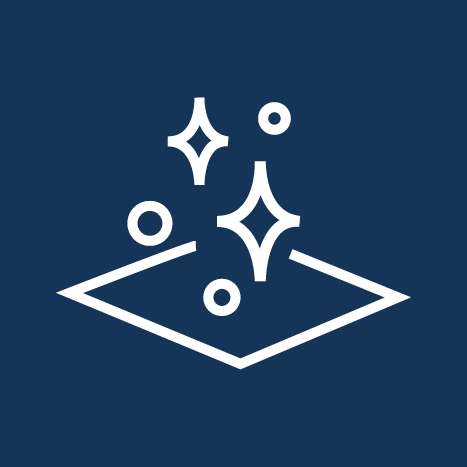
Technical cleaning
Pre-cleaning
Equipment
Notes
Steam cleaning
Elmasteam 8 basic steam cleaner
Steam cleaning, particularly suitable for cleaning blind holes, for removing chips, and for pre-cleaning
Cleaning bath with deionized water
For rinsing off cutting fluid and maintaining the quality of the ultrasonic cleaning bath
Ultrasonic cleaning bath with cleaning agent
Elmasonic Select 900
Cleaning bath with a 65-l capacity for parts up to 550 x 460 mm. Cleaning agent used: Olschner Optimal 9.5
Cleaning bath with deionized water
For rinsing off the cleaning agent
Hot-air drying
Elmadry TD 300
For complete drying without stains
Pre-cleaning
Equipment
Notes
Ultrasonic cleaning bath with cleaning agent
Elmasonic Select 900
Cleaning bath with a 65-l capacity for parts up to 550 x 460 mm. Cleaning agent used: Olschner Optimal 9.5
Ultrasonic cleaning bath without cleaning agent
Elmasonic Select 900
Cleaning bath with a 65-l capacity for parts up to 550 x 460 mm. For rinsing off the cleaning agent.
Hot-air drying
Elmadry TD 300
For complete drying without stains
UV and white-light check
Final check for stains and organic or anorganic soiling.
Facts & figures
- Pre-cleaning – within 30 minutes
- Final cleaning – with white light and UV check
- Part size – 500 x 2300 x 2500 mm
Our technical cleaning
Our cleaning of parts is divided into pre-cleaning and final cleaning to ensure that your parts are spotlessly clean.
After the parts come out of a machine that uses HIO-free cutting fluid, they run through pre-cleaning within 30 minutes.
When the parts have been checked and measured, they undergo final cleaning with additional ultrasonic cleaning and hot-air drying. The final UV light check ensures that the parts are spotless.
For large parts, we are planning to invest in a cleaning container in 2024 to enable us to effectively clean and dry even parts up to a size of 500 x 2300 x 2500 mm.
Clean parts are crucial for manufacturing high-precision quality products and our cleaning processes guarantee thorough removal of residue for optimum results.
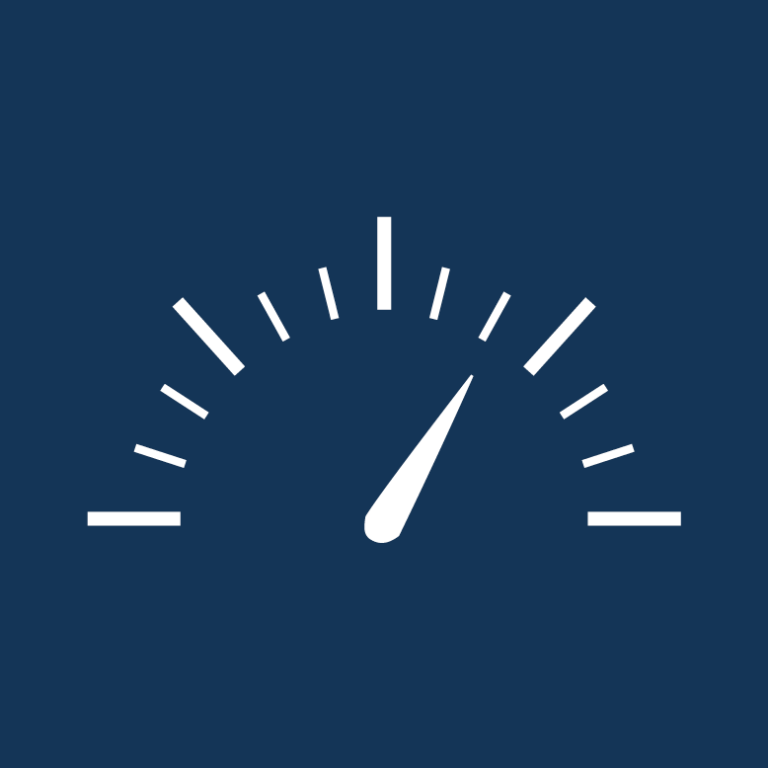
Measuring and test equipment
Coordinate measuring machines
X
Y
Z
ZEISS Prismo 16/30/10
1.600
3.000
1.000
MITUTOYO Crysta-Apex
900
1.600
800
FaroArm Platinum
Static mount
Measuring radius 1.85 m
3.700
Customer-specific tests, e.g.
Insulation checks
Pressure tests with nitrogen or water
Vacuum tests & leak tests
Other measuring and test equipment
Keyence XM-T1000: measuring range 600 x 500 x 200
MITUTOYO Profile Projector PV-5100 with QM-Data 200 data processor
MITUTOYO SJ-400 surface roughness tester
Surftest surface roughness tester MarSurf PS 10
MITUTOYO height gage LH 600 E 2x
SPECTRO Spectrotest JR spectral analysis device
Krautkrämer Branson hardness tester “Microdur II”
Vacuum testing unit (10-8 spray test, integral test HV 1), test unit: Leybold Phoenix L300i / Pfeiffer Vacuum ASM 340
Facts & figures
- Coordinate measuring machines
- Customer-specific tests
Our quality promise
We promise not only quality, but also document it based on verifiable criteria. To ensure this, we have equipped out manufacturing department with state-of-the-art measuring and test equipment. We use a number of measuring parameters to comprehensively check parts and systems and to log all results accurately. We always supply you with transparent quality documentation.
We use our measuring and testing competence not only for the components manufactured by us, but also for your products if requested. Talk to us about which tests you would like us to carry out.
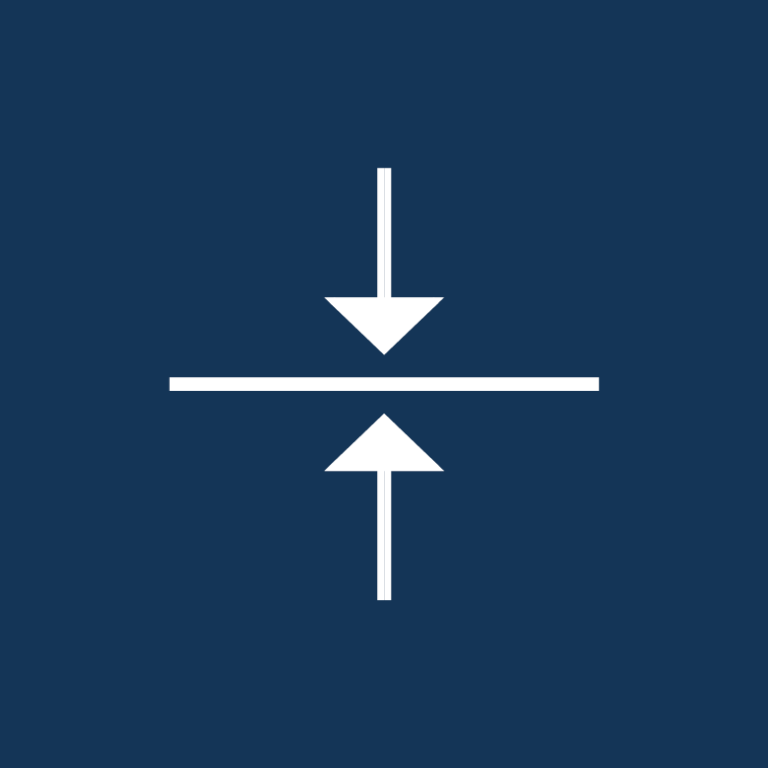
Straightening
Steady hands, inner calm, and a wealth of experience are essential in this special area of manufacturing.
If geometries deviate minimally from the design due to tensions in the raw material, we make the necessary corrections to ensure that guide rails, frames, and supports achieve geometrical perfection. It is only with straightening that we can achieve the maximum performance potentials of your machines for yourself and for your customers.
Straightening increases the wear resistance of your machine parts and therefore the process quality. For high-speed processes in particular, straightening is a success factor because it ensures smooth running of rapidly rotating parts.
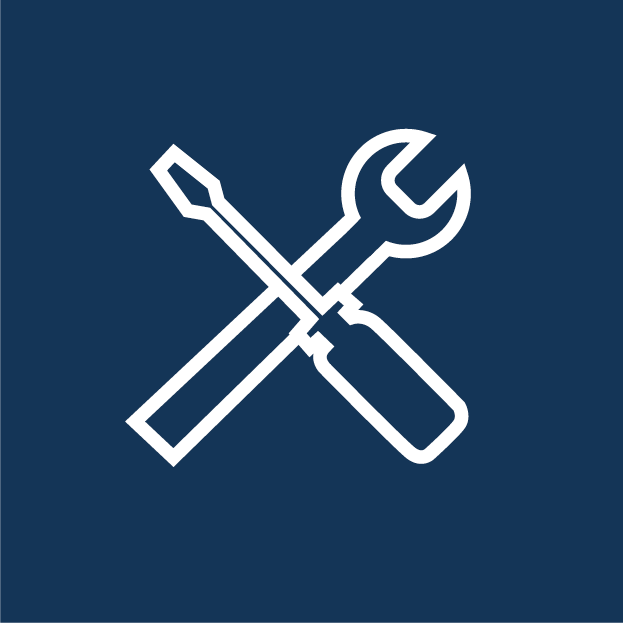
Assembly
Facts & figures
- Flexible – project areas
- Optimized – for series assembly
Our assembly shop
On over 3700 square meters, our production team assemble mechanical and electromechanical assemblies. We have set up flexible, expandable project areas for this. For large quantities or series deliveries, we use the one-piece flow model.
What sets us apart: 100 % of our workers are qualified specialists. Because quality has a lot do with qualification as well.
If required, we carry out assembly in a cleanroom (ISO 7) and meet our customers’ cleanliness requirements. In the first half of 2024, we want to start running our laminar flow box with category ISO 6-5.
Assembly at WASSERMANN is always a clean affair.
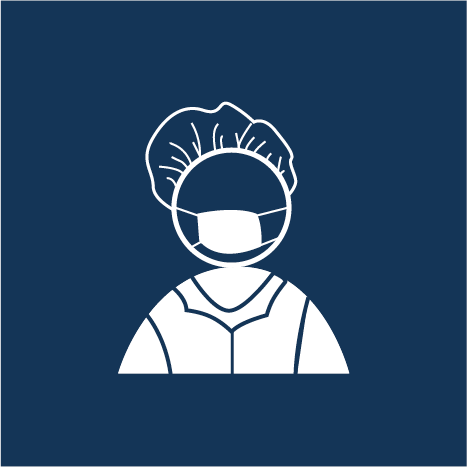
Cleanroom assembly
Facts & figures
- Area – 7 x 7 m
- Category – ISO 7-5
Our cleanroom assembly
Our customized cleanroom assembly services offer an optimum environment for projects with the highest cleanliness requirements.
We can handle even large projects with a cleanroom size of around 7 x 7 m. Even weights up to 1000 kg are not a problem.
Adjustments and checks are carried out with the greatest care in order to meet cleanliness requirements. Our cleanroom complies with ISO category 7 to enable optimum results for customers from the semiconductor and display industry.
For particularly challenging cleanliness requirements, we additionally offer a laminar flow bank that can achieve cleanroom category ISO 5 in ideal conditions. With low-turbulence displacement ventilation, we meet even the highest cleanliness standards.
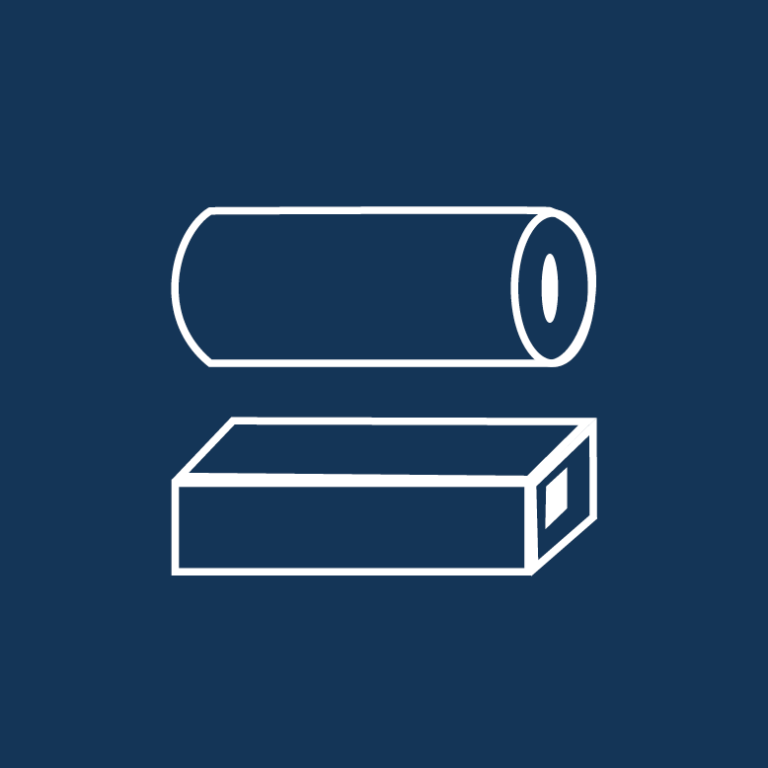
Materials
Facts & figures
- Metal machining
We work with everything that looks like metal
Our manufacturing department gets a number of materials into perfect shape.
In addition, we give 3-D printed metal parts the final touch with precision post processing.
There is one material that we do not machine, though: plastic. But we have several partners in our network who are excellent at this.
We just love the sound of metal.
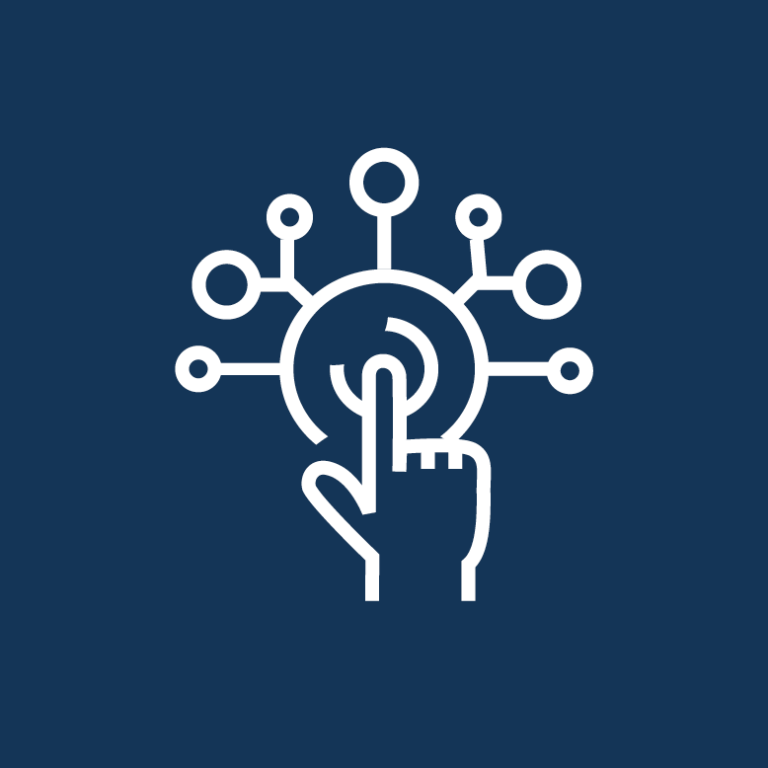
Digitalization
We know what is going on in our production and when, because our manufacturing department is fully transparent at all times thanks to state-of-the-art digitalization.
We keep an eye on each machine and its availability in real time. We conduct downtime monitoring and performance monitoring and can therefore plan accurately and can offer our customers reliable deadlines and challenging parts at attractive prices.